Webinar
Webinars on the topic of column diagnostics
We would like to offer you webinars on column diagnostics at loose intervals.
The first webinar took place on October 26, 2023. It was led by Mr. Thomas Esper with the support of an expert in thermal separation processes, Prof. Dr.-Ing. Till Adrian, Professor at the Mannheim University of Applied Sciences.
Please check our website regularly to find out when the next webinar starts!
Webinar
Wie Kolonnendiagnostik die Verfügbarkeit und Effizienz Ihrer Anlagen verbessert
Kolonnendiagnostik hat für den Betreiber Vorteile:
- Die Verfügbarkeit der Anlagen wird planbarer.
- Der Umfang und die Kosten von Stillständen können deutlich reduziert werden.
- Die Energieeffizienz kann deutlich erhöht werden.
Das Webinar findet am 26.10.2023 von 11 bis 12 Uhr über Microsoft Teams statt.
Hier können Sie sich zum Webinar anmelden
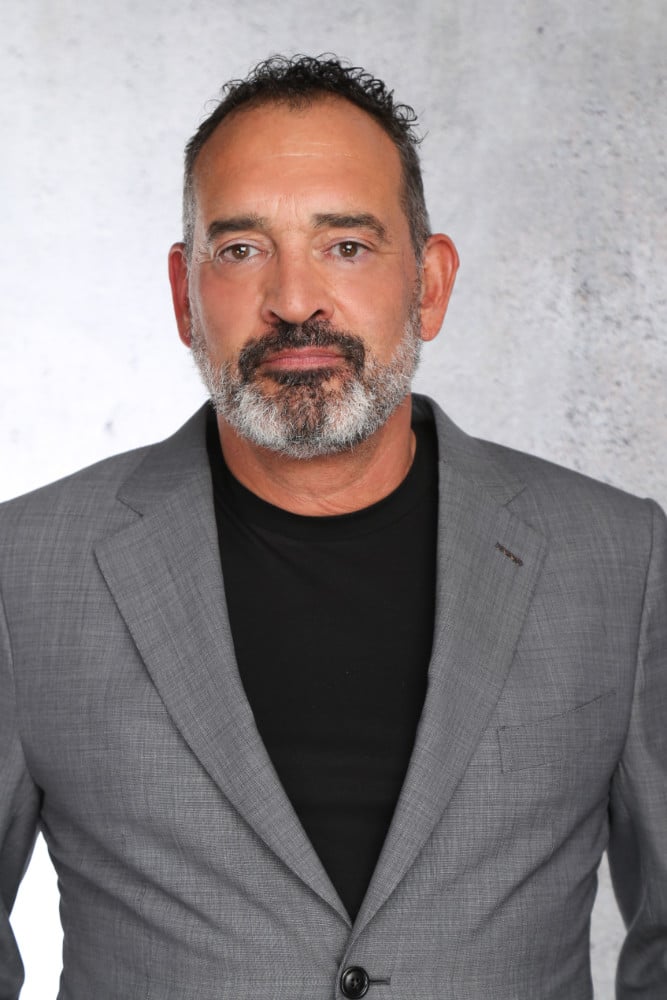
Geleitet wird das Webinar von Thomas Esper, IBE Ingenieurbüro Esper GmbH.
LinkedIn-Profil
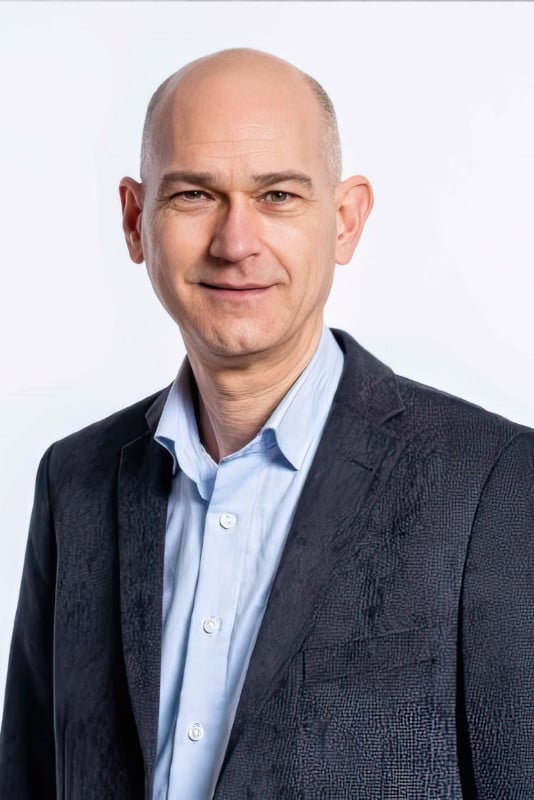
Als Spezialisten auf dem Gebiet der „Thermischen Trennverfahren“ konnten wir
Herr Prof. Dr.-Ing. Till Adrian, Professor an der Hochschule Mannheim, gewinnen.
Read our specialist articles on past webinars
How column diagnostics improve the availability and efficiency of your systems (26.10.2023)
Part 1: Shutdown planning and preparation
The smooth operation of an industrial plant is the goal of every plant engineer/plant manager. Ideally, the plant should continuously output a high-quality product. Unfortunately, this is not always the case. Wear and tear, fouling, process-related issues, fluctuations in raw material quality—many factors can affect production and product quality without being immediately detectable.
As a result, manufacturing facilities periodically shut down to inspect the mechanical integrity of equipment and the degree of fouling in internals, and to carry out any necessary repairs. Oftentimes, these shutdowns are legally mandated at regular intervals. With the help of our gamma scanning technology and in consultation with the relevant regulatory authorities, it’s possible to avoid costly column inspections if our analysis confirms the mechanical integrity of internals and column shell.
By conducting a column scan prior to a shutdown, the following points can be clarified within just one day:
• Is it necessary to open/inspect the affected column at all?
•Which replacement parts for damaged internals should be ordered? Delivery times must be considered.
• Are the currently installed internals optimal for this process, or are there more efficient solutions?
Clarifying these points prior to shutdown allows for better planning. Replacement parts or new internals can be ordered in advance without time pressure or urgency surcharges. Unexpected extensions of the shutdown can be avoided.
Operators gain the following:
• Loss minimization.
• Increased bargaining power over suppliers.
• Reduction in the scope of shutdown, if scans confirm there’s no need to shut down specific plant components.
• By monitoring the degree of fouling, emergency shutdowns can be avoided, as column scans enable early detection of hydraulic limitations in the columns.
• All of this results in optimized plant availability.
With our expertise and many years of experience in troubleshooting distillation plants, we are more than happy to support you in planning your shutdown.
Part 2: Reduction of costs and scope of shutdown
Plants are subject to regular shutdowns, partly due to regulatory requirements. We will outline some aspects of how you can strategically plan your shutdowns, reduce the scope of shutdowns, or postpone them by implementing suitable measures.
Monitoring fouling-prone plants can allow extended intervals between shutdowns. Regular measurement with our gamma scanning technology allows documentation and evaluation of the degree of fouling. Sometimes, flushing the plant can suffice for a short period of time. Additionally, hot tapping can be an option, as our measurements can determine the exact position of the blockage. Shutdowns can be planned more thoroughly, but, above all, emergency shutdowns can be avoided altogether.
In the chemical industry, there are systems where opening the equipment entails significant effort. Plants where toxic raw materials/products are present require extensive flushing, or if self-igniting substances are present, inertization is necessary. In these cases, our diagnostics can avoid the need to open the system altogether, as the operator receives a factual assessment of the condition of plant components.
Bei Prozessen, die durch ein Verbundsystem von Kolonnen bewerkstelligt werden, können durch eine Vermessung aller Anlagen die Schwachstellen ausfindig gemacht werden, sodass sich der Stillstand und die entsprechende Wartung auf diese konzentrieren kann.
In integrated facilities, measuring all equipment can identify weaknesses, allowing the corresponding maintenance to focus on areas of trouble. Checking the mechanical integrity after incidents such as start-up problems, steam hammer, or power outages, can localize the affected areas and help with targeted damage repair.
A column scan can be used to determine how the process is impacted by changes, such as the use of a new catalyst carrier or the purchase of raw materials from another source.
In all cases, our gamma scanning technology enable cost savings which greatly benefit operators.
With a column scan you can:
• extend the interval between shutdowns,
• reduce the scope of the standstill,
• set the focus on critical components,
• significantly minimize downtime,
• reduce costs significantly.
With our expertise and many years of experience in troubleshooting distillation units, reactors, and heat exchangers, we are more than happy to assist you in planning your shutdown.
Part 3: Increasing energy efficiency
Distillation plants are high-energy-consuming facilities. In the current economic situation, energy costs have an even greater impact. Column diagnostics help in finding energy-saving potential.
A crucial aspect of maximizing energy efficiency is ensuring optimal operation of the plant. If the plant shows deficiencies, such as failure to achieve product quality and/or yield, parameters are adjusted, which can increase costs, such as
• increased steam input,
• increased reflux, resulting in more liquid needing to be vaporized.
By increasing pressure, steam volume can be reduced. However, this impacts the static load on the column shell and its periphery, thus affecting the lifespan of components.
By reducing vacuum pressure, better evaporation can be achieved at lower temperatures, but physical limits and the cost factor must be considered.
Both measures can lead to excessive liquid and vapor loads that can flood the column. This needs to be avoided. Limiting flow rates can lead to situations in which, to achieve the required quality, the product must be temporarily stored in a vessel before later being reintroduced into the process. This increases specific energy costs significantly.
Our column diagnostics services can determine whether the plant is operating at its optimal operating point. We assess whether the internals are in good mechanical condition and whether fluid dynamic anomalies such as liquid entrainment, flooding of the active tray area or downcomer, or maldistribution are present.
The initial on-site evaluation provides insights into,
• the presence of the described anomalies in the internals,
• whether too much liquid is entrained,
• the liquid level in the sump and its correlation with internal level measurements,
• whether, in columns with multiple feed points, this area is partially hydraulically overloaded due to insufficient feed temperatures.
Conclusions about the degree of fouling of the internals can be drawn by correlating the results of the hydraulic calculations with the scan results.
The advantage of gamma scanning technology for the operator is that the measurement is carried out during operation. With the insights gained, we can help you optimize energy efficiency and reduce costs.