Webinar
Webinare rund um das Thema der Kolonnendiagnostik
In losen Abständen möchten wir Ihnen Webinare anbieten für den Bereich Kolonnendiagnostik.
Das erste Webinar fand am 26.10. 2023 statt. Geleitet wurde es von Herrn Thomas Esper mit Unterstützung eines Fachmanns der Thermischen Trennverfahren, Herrn Prof. Dr.-Ing. Till Adrian, Professor an der Hochschule Mannheim.
Schauen Sie gerne regelmäßig auf unserer Webseite vorbei, um zu erfahren, wann das nächste Webinar startet!
Webinar
Wie Kolonnendiagnostik die Verfügbarkeit und Effizienz Ihrer Anlagen verbessert
Kolonnendiagnostik hat für den Betreiber Vorteile:
- Die Verfügbarkeit der Anlagen wird planbarer.
- Der Umfang und die Kosten von Stillständen können deutlich reduziert werden.
- Die Energieeffizienz kann deutlich erhöht werden.
Das Webinar findet am 26.10.2023 von 11 bis 12 Uhr über Microsoft Teams statt.
Hier können Sie sich zum Webinar anmelden
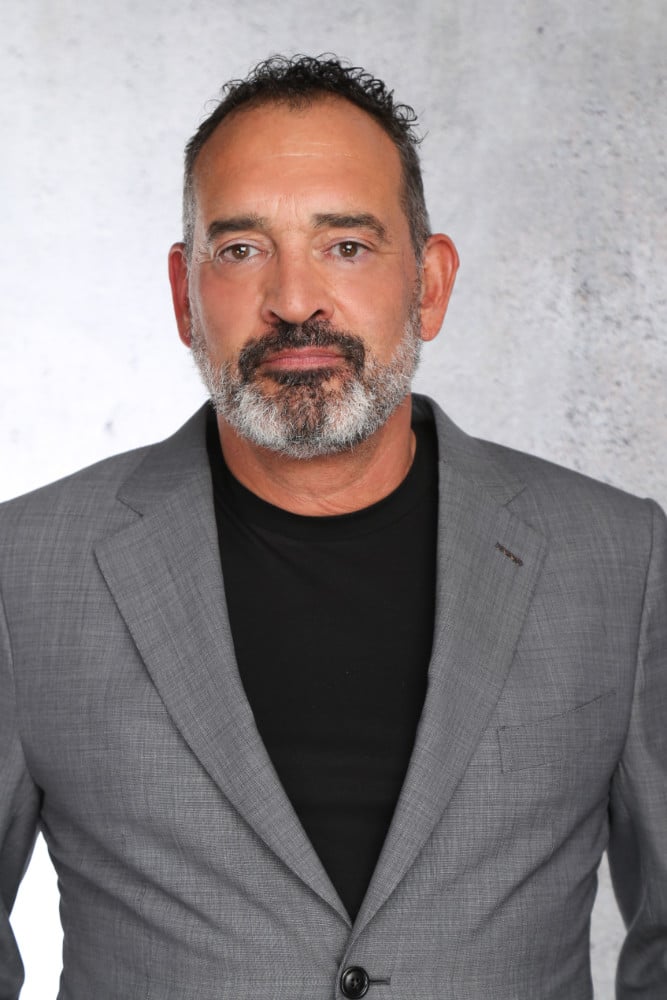
Geleitet wird das Webinar von Thomas Esper, IBE Ingenieurbüro Esper GmbH.
LinkedIn-Profil
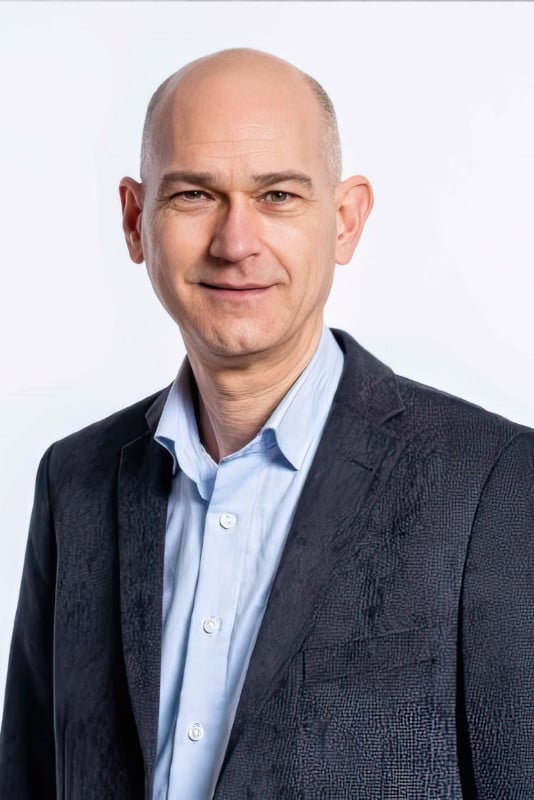
Als Spezialisten auf dem Gebiet der „Thermischen Trennverfahren“ konnten wir
Herr Prof. Dr.-Ing. Till Adrian, Professor an der Hochschule Mannheim, gewinnen.
Unsere Fachartikel zu vergangenen Webinaren zum Nachlesen
Wie Kolonnendiagnostik die Verfügbarkeit und Effizienz Ihrer Anlagen verbessert (26.10.2023)
Teil 1: Stillstandsplanung und -vorbereitung
Der reibungslose Betrieb einer industriellen Anlage ist das Ziel jeden Betriebsingenieurs/Betriebsleiters. Idealerweise soll die Anlage ununterbrochen ein verkaufsfähiges Produkt liefern. Das ist in der Realität leider nicht immer der Fall. Verschleiß, Verschmutzung, verfahrenstechnische Probleme, Qualitätsschwankungen der Einsatzstoffe, viele Faktoren können die Produktion und die Produktqualität beeinträchtigen, ohne dass es sofort erkannt und lokalisiert werden kann.
Die produzierenden Betriebe gehen daher in regelmäßigen Abständen in den Stillstand, dabei soll die mechanische Integrität der Apparate, sowie der Verschmutzungsgrad der Einbauten überprüft und gegebenenfalls korrigiert werden. Sehr oft sind Stillstände in regelmäßigen Abständen behördlich vorgeschrieben. Mit der Hilfe unserer Messungen können unter Umständen in Absprache mit den zuständigen Aufsichtsbehörden aufwendige Kolonnenbegehungen vermieden werden, wenn durch unsere Analyse die mechanische Integrität der Einbauten und des Kolonnenmantels sichergestellt ist.
Mit einem Kolonnenscan können im Vorfeld eines Stillstands innerhalb eines Tages folgende Punkte geklärt werden:
• Muss man die betroffene Kolonne überhaupt öffnen/begehen?
• Sollen Ersatzteile für beschädigte Einbauten oder komplett neue Einbauten bestellt werden? Dabei sind die Lieferzeiten zu beachten.
• Sind die derzeit eingesetzten Einbauten optimal für diesen Prozess oder gibt es effizientere Lösungen?
Mit der Klärung dieser Punkte kann besser geplant werden. Ersatzteile oder neue Einbauten können ohne Zeitdruck und Dringlichkeitszuschlag bestellt werden. Der Zeitrahmen des Stillstands wird nicht unvorhersehbar ausgedehnt.
Folgende Vorteile ergeben sich für die Betreiber:
• Minimierung des Wertschöpfungsverlusts.
• Bessere Verhandlungsposition mit den Lieferanten.
• Reduzierung des Umfangs des Stillstands, wenn keine Notwendigkeit der Abstellung von bestimmten Anlagenteilen festgestellt wird.
• Durch Monitoring des Verschmutzungsgrades können Notstillstände vermieden werden, da mit einem Kolonnenscan eine Früherkennung der Limitierungen in den Kolonnen möglich ist.
• Daraus resultiert dann eine optimierte Anlagenverfügbarkeit, die nicht durch unerwartete Zeitverzögerungen verschlechtert wird.
Mit unserer Expertise und langjähriger Erfahrung im Troubleshooting der Destillationsanlagen unterstützen wir Sie sehr gerne bei der Planung Ihres Stillstandes.
Teil 2: Reduktion des Stillstandumfangs und der damit verbundenen Kosten
Anlagen werden regelmäßigen Stillständen unterzogen, zum Teil sind die Fristen behördlich vorgegeben. Wir zeigen Ihnen einige Aspekte auf, wie Sie Ihre Anlagen zielgerichteter stillstehen lassen können, den Umfang des Stillstands reduzieren können oder den Zeitpunkt durch geeignete Maßnahmen nach hinten schieben können. Der Abstand der Stillstände kann bei verschmutzungsanfälligen Anlagen durch Monitoring verlängert werden. Bei regelmäßiger Messung mit unserer Gammastrahlentechnologie kann der Grad der Verschmutzung dokumentiert und damit eingeschätzt werden. Übergangsweise können Spülaktionen das Mittel der Wahl sein. Auch ein Hot Tapping kann eine Alternative sein, denn mit unserer Hilfe kann die Position der Blockade ermittelt werden. Der Stillstand kann nach Bedarf geplant werden, aber vor allem können Notabschaltungen vermieden werden. In der chemischen Industrie gibt es Systeme, bei denen das Öffnen der Apparate mit großem Aufwand verbunden ist. Toxische Einsatzstoffe/Produkte erfordern langes Spülen im Vorfeld oder Stoffe und Ablagerungen, die durch Luftsauerstoff/Luftfeuchtigkeit selbstentzündlich sind, machen langes Inertisieren der Apparate vor dem Öffnen nötig. Auch hier kann die Diagnostik unter Umständen ein Öffnen vermeiden, da Sie dann als Betreiber eine faktische Beurteilung des Zustandes Ihrer Anlage/Anlagenteile erhalten. Bei Prozessen, die durch ein Verbundsystem von Kolonnen bewerkstelligt werden, können durch eine Vermessung aller Anlagen die Schwachstellen ausfindig gemacht werden, sodass sich der Stillstand und die entsprechende Wartung auf diese konzentrieren kann. Die Überprüfung der mechanischen Integrität nach Vorfällen wie Anfahrprobleme, Dampfschläge oder Stromausfall kann die betroffenen Stellen lokalisieren und bei der gezielten Schadensbehebung behilflich sein. Ob Änderungen im Verfahren, wie der Einsatz eines neuen Katalysatorträgers oder der Bezug von Rohstoffen aus anderer Quelle, Auswirkungen auf den Prozess haben, kann durch einen Kolonnenscan festgestellt werden. Der Vorteil für Sie als Betreiber ist in jedem Fall eine Kostenersparnis. Die Kosten der Messung sind in der Regel eine Größenordnung geringer als die eingesparten Kosten. Mit einem Kolonnenscan kann: • der Abstand zwischen den Stillständen verlängert werden, • der Umfang des Stillstands reduziert werden, • der Fokus auf kritische Anlageteile gelegt werden, • der Produktionsausfall erheblich minimiert werden, • eine signifikante Senkung der Kosten erreicht werden. Mit unserer Expertise und langjähriger Erfahrung beim Vermessen von Destillationsanlagen, aber auch von Reaktoren und Wärmetauschern, unterstützen wir Sie sehr gerne bei der Planung Ihres Stillstandes. > Fachartikel als PDF herunterladenTeil 3: Erhöhung der Energieeffizienz
Destillationsanlagen sind Anlagen mit hohem Energieverbrauch. Die Kosten schlagen in der aktuellen Wirtschaftslage noch stärker zu Buche. Hier gilt es, nach Einsparpotentialen zu suchen.
Wichtig im Hinblick auf größtmögliche Energieeffizienz ist eine optimal laufende Anlage. Zeigt die Anlage Defizite, wie das Nichterreichen der Produktqualität und/oder der Ausbeute, werden Parameter geändert, die den Kostenfaktor in die Höhe treiben, wie
• höherer Dampfeinsatz,
• Erhöhung des Rücklaufs, wobei mehr Flüssigkeit verdampft werden muss.
Durch die Erhöhung des Drucks kann das Dampfvolumen reduziert werden. Dies hat Auswirkungen auf die statische Belastung des Kolonnenmantels und dessen Peripherie und damit auf die Lebensdauer der Bauteile.
Durch die Erhöhung des Vakuums kann eine bessere Verdampfung bei niedrigeren Temperaturen erfolgen, doch auch hier sind physikalische Grenzen und der Kostenfaktor zu berücksichtigen.
Bei diesen Maßnahmen muss vermieden werden, dass die Flüssigkeits- und Dämpfebelastung zu hoch wird und die Kolonne flutet. Aus der Limitierung der Mengenströme kann eine Situation entstehen, dass das Produkt mit unzureichender Qualität in einem Behälter zwischengelagert werden muss und dann zusammen mit den Edukten nochmal in den Prozess zurückgeführt wird. Erst dann wird die benötigte Qualität erreicht. Die spezifischen Energiekosten steigen dementsprechend.
Ob die Anlage tatsächlich an ihrem optimalen Betriebspunkt läuft, kann eine Überprüfung mittels Kolonnendiagnostik zeigen. Dabei wird festgestellt, ob die Einbauten in einwandfreiem mechanischem Zustand sind und ob fluiddynamische Anomalien wie Flüssigkeitsmitriss, Flutungen der aktiven Bodenfläche oder der Schächte vorliegen oder Maldistributionen vorhanden sind.
Die erste Auswertung noch vor Ort liefert Erkenntnisse,
• ob die oben beschriebenen Anomalien der Einbauten vorliegen,
• ob Flüssigkeit über Kopf mitgerissen wird,
• wie hoch der Füllstand im Sumpf liegt, und wie die betriebsinterne Standmessung damit korreliert,
• ob bei Kolonnen mit mehreren möglichen Zulaufstellen dieser Bereich durch zu geringe Zulauftemperaturen partiell hydraulisch überlastet ist.
Rückschlüsse auf den Verschmutzungsgrad der Einbauten erhält man, wenn man das Ergebnis der hydraulischen Berechnungen mit den Scanergebnissen in Korrelation setzt.
Der Vorteil für den Betreiber einer Kolonnendiagnostik mit Gammastrahlung ist, dass die Messung im laufenden Betrieb durchgeführt wird. Mit den gewonnenen Erkenntnissen helfen wir Ihnen den Energieverbrauch zu optimieren und dadurch Kosten zu senken.
> Fachartikel als PDF herunterladen